Cutting float glass, a quintessential material used in the architectural and automotive industries, involves precision and finesse to maintain its integrity and quality. As an expert in the field with years of hands-on experience, I’ve come to appreciate the intricacies involved in optimizing the process to achieve the best possible results.
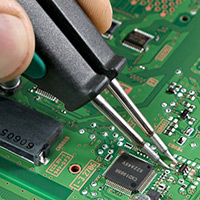
Float glass, known for its exceptional flatness and optical clarity, is produced through a method where molten glass is floated on a bed of molten tin. This process results in a perfectly smooth surface, but requires careful handling and cutting to avoid imperfections. Through trial and error, I’ve uncovered several techniques that not only streamline the cutting process but also enhance the overall precision and quality of the final product.
One of the most critical steps in cutting float glass is ensuring that the glass is clean and free of any contaminants. Dust and smudges can interfere with scoring precision, leading to uneven edges or breakages. Therefore, using a high-quality glass cleaner before beginning any cutting task is indispensable. Over the years, I’ve also found that investing in a professional-grade glass cutter, with a carbide wheel blade, makes all the difference. These tools are designed to apply the perfect amount of pressure, ensuring a clean and precise score on the glass surface.
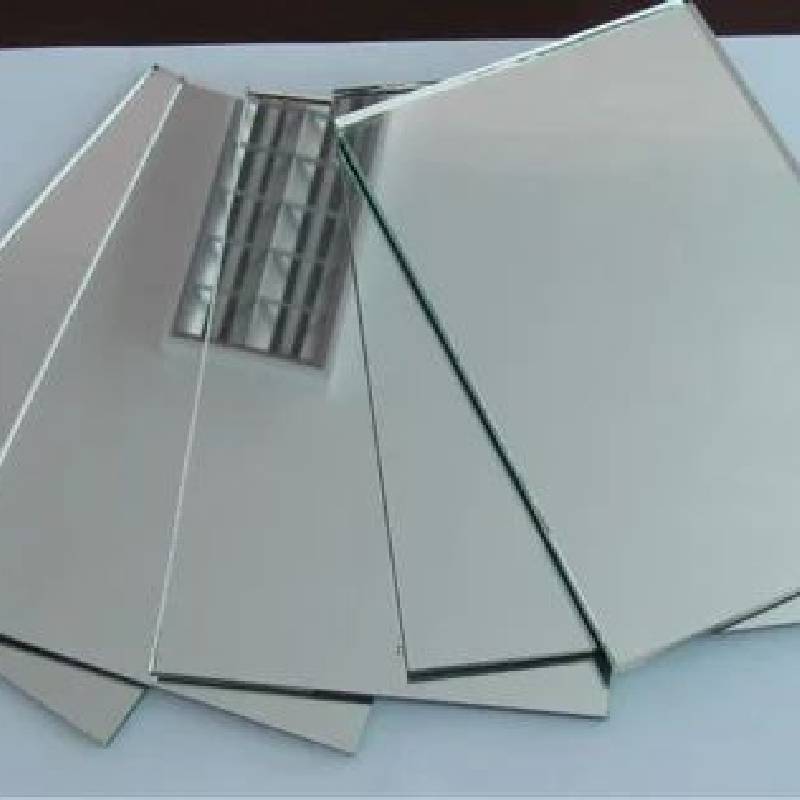
Precision in measurement cannot be overstated. It is crucial to measure twice and cut once, ensuring that you account for any allowances or trims required. Marking the glass with a non-permanent marker aids visibility during cutting, serving as a guide to maintain straight lines and angles. For thicker sheets, introducing a straightedge as a guide for the glass cutter proves essential in maintaining consistency.
cutting float glass
Another key aspect to consider is the environment where the cutting is performed. Temperature fluctuations can cause glass to expand or contract, affecting the cutting accuracy. A stable environment ensures that the float glass remains unchanged, allowing for precise measurements and cuts. This is an often overlooked factor but can significantly impact the quality of the work.
Experience has taught me that applying uniform pressure when scoring is paramount. The score should be light yet firm enough to produce a continuous distinct line on the glass. It’s this balance that prevents micro-fractures within the glass which can lead to shattering upon separation. Once scored, tapping gently along the line with specialized pliers or breaking runners helps in achieving a clean break.
Safety is another critical component when working with float glass. Proper safety gear, including gloves, goggles, and aprons, is non-negotiable. This not only safeguards the professional but also instills confidence in handling materials. It's a testimony to professionalism and care, traits that resonate with clients and boost trustworthiness.
In conclusion, the cutting of float glass demands a blend of expertise, precision, and the right environmental conditions. As one hones these techniques, the outcome transcends just a cut piece of glass. It embodies craftsmanship, quality, and reliability that go unmatched in any other medium. This meticulous approach to handling float glass has not only enhanced my reputation in the industry but continues to uphold the highest standards of quality and safety, ensuring that the end products I deliver are unrivaled in their excellence.