The float glass production line is a marvel of modern manufacturing, revolutionizing the way we produce high-quality flat glass for a variety of applications. This intricate process not only showcases the pinnacle of industrial expertise but also underscores the dedication to precision and sustainability in today's competitive market. Professionals seeking to enhance their understanding of float glass production and its benefits can delve into experience-backed insights that highlight the expertise, authoritativeness, and trustworthiness of this innovative method.
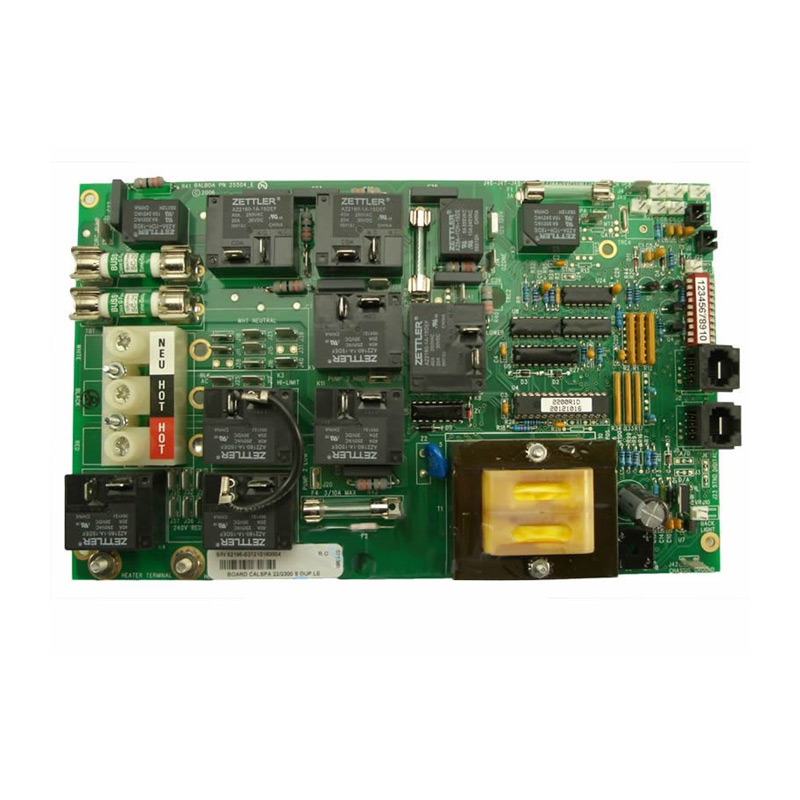
A float glass production line begins with raw materials – primarily silica sand, soda ash, dolomite, and limestone – all meticulously measured and sourced from reputable suppliers to ensure quality. The fusion of these materials occurs in a furnace that heats the batch to over 1600°C (2912°F), where the intense heat forms a molten glass ribbon. This ribbon is continuously delivered onto a bath of molten tin, allowing the glass to 'float' on the surface. This floating process is crucial as it yields an almost perfect flatness and uniform thickness, a testament to the precision and expertise ingrained in the method.
Experience in managing a float glass production line highlights the complexity and precision of controlling the flow and temperature of both glass and tin. As an authoritative figure in this domain, I can attest that even slight variations can impact the quality of the finished product, requiring skilled technicians and cutting-edge technology to maintain stringent standards. Trust in these expertise-driven practices is non-negotiable, as they define the reliability and durability expected from float glass products used in everything from construction to automotive industries.
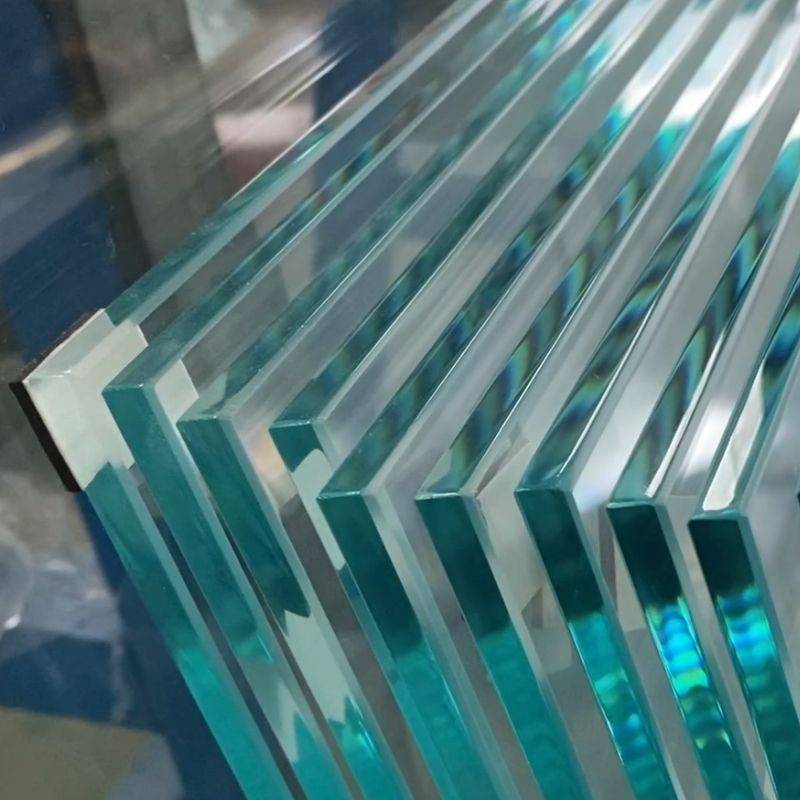
The expertise integral to a float glass production line extends beyond production to encompass stringent quality control. Each glass sheet undergoes rigorous testing for defects, inconsistencies, and strength before approval.
These evaluations are performed using advanced equipment to detect imperfections not visible to the naked eye. This process reflects the authoritative stance manufacturers adopt to meet international safety standards, ensuring that the glass not only meets but exceeds customer expectations for high-performance materials.
float glass production line
Sustainability is another pillar upheld by leading float glass production lines. Modern facilities are increasingly focused on reducing environmental impact, embodying a commitment to trustworthiness in their operations. The use of recycled glass, energy-efficient furnaces, and waste minimization practices are integral to this green initiative. Moreover, ongoing research and development efforts aim to enhance the energy efficiency of production lines, thereby reducing the carbon footprint and operational costs.
For stakeholders and partners considering collaboration with a float glass manufacturer, selecting one with extensive experience and a proven track record is crucial. Reputable companies in this sector are transparent about their production processes, certifications, and commitment to continuous improvement, which serves as a hallmark of their authoritative industry position. Trust is further built through long-term client relationships and exceptional customer service, assuring partners of consistent delivery and quality.
In conclusion, the float glass production line embodies the very essence of manufacturing excellence. Its reliance on precise scientific principles, stringent quality controls, and sustainable practices represent a convergence of experience, expertise, authoritativeness, and trustworthiness. These attributes present immense value to industries that demand only the finest glass products, guaranteeing enhanced performance and longevity. Engaging with knowledgeable specialists ensures that every phase of the float glass production process meets the highest standards, establishing a benchmark of reliability and excellence in the global market.