Shaping the future of architecture and design, float glass stands as a cornerstone in modern construction and interior aesthetics. The precise engineering involved in float glass cut to size transforms standard glass sheets into bespoke solutions for a myriad of applications. This article delves into the intricate journey of float glass from production to installation, exploring its exceptional qualities and the expertise required to tailor it to individual needs.
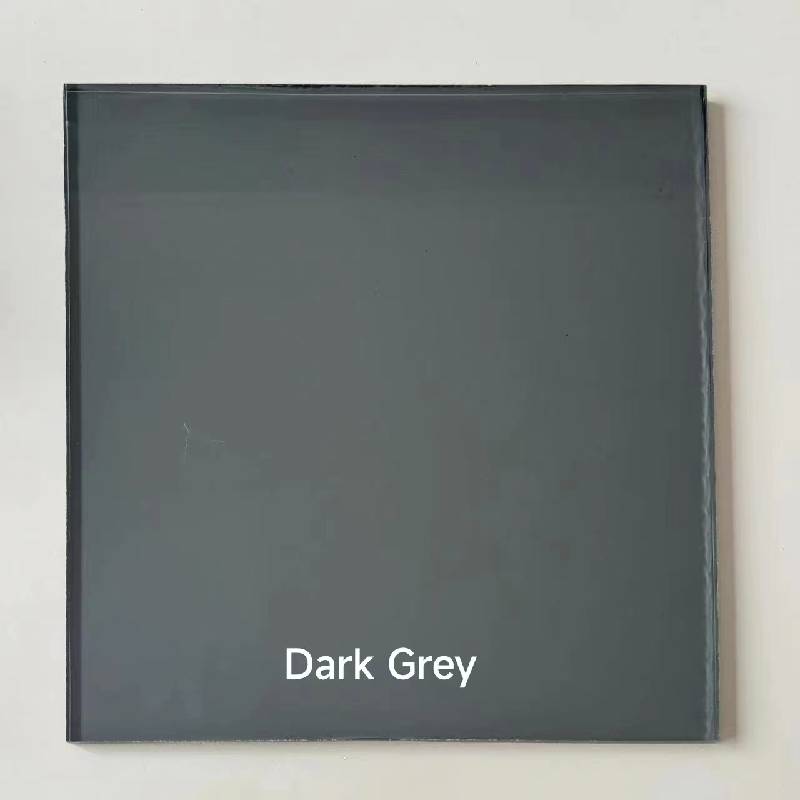
Float glass, a marvel of 20th-century innovation, is produced by floating molten glass on a bed of molten tin, resulting in perfectly flat and uniform sheets. This method not only guarantees a flawless surface but also enhances the material's optical quality, making it the preferred choice for architectural projects worldwide. Cutting float glass to size, however, requires a blend of advanced technology and skilled craftsmanship to maintain its integrity and achieve the desired dimensions.
A key advantage of float glass is its versatility. It can be customized to fit any space or design requirement, from residential windows and doors to intricate architectural features in commercial buildings. The process begins with precise measurements and continues with the exact cut to the specified size. This customization allows architects and designers to push creative boundaries while ensuring that the glass seamlessly integrates into the given environment.
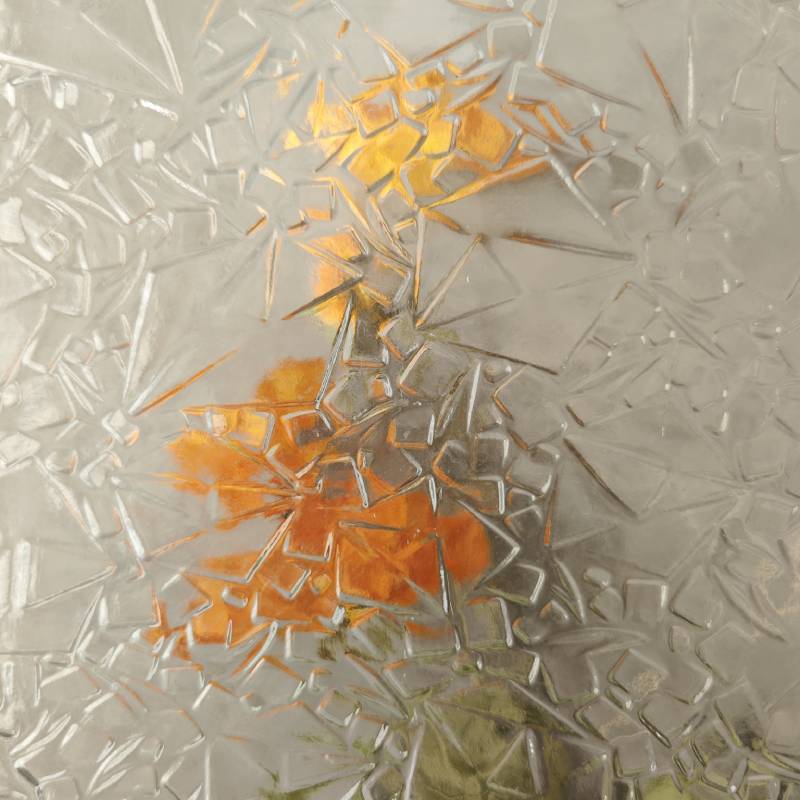
Once the measurements are confirmed, cutting float glass to size involves the use of state-of-the-art equipment. Computer Numerical Control (CNC) machines equipped with diamond-tipped blades enable precise cuts, accommodating complex shapes and sizes with minimal margin for error. This precision is crucial, especially for installations that require tight tolerances, ensuring that each piece fits perfectly and performs optimally.
The expertise involved in handling and cutting float glass cannot be understated. Technicians must possess a deep understanding of the material's properties, including its strength, flexibility, and potential weaknesses. This knowledge is pivotal in avoiding common pitfalls, such as chipping or cracking, which can compromise the glass's performance and aesthetics. Additionally, proper storage and handling techniques are integral to maintaining the quality and durability of the glass throughout the cutting process.
float glass cut to size
Beyond the technical precision, the application of float glass cut to size must adhere to stringent safety and quality standards. For instance, tempered or laminated options may be necessary for safety glass applications, enhancing both the durability and shatter resistance. This additional processing not only ensures compliance with safety regulations but also extends the lifespan of the product, offering greater value to end-users.
Trustworthiness in the industry further strengthens the float glass market's position. Reputable manufacturers and suppliers are committed to delivering high-quality products consistently, coupled with reliable customer service. This dedication is evident in their adherence to best practices, rigorous quality control, and their readiness to provide expert guidance tailored to each project’s specific needs.
In terms of installation, float glass cut to size simplifies the process dramatically. With pre-cut dimensions, onsite adjustments are minimized, reducing installation time and labor costs. This efficiency appeals to contractors and homeowners alike by ensuring a smooth, hassle-free installation that aligns with project timelines and budgets.
Environmental considerations also play a significant role in the production and modification of float glass. Sustainable manufacturing processes and the recyclability of glass make it an eco-friendly choice. Additionally, innovations in energy-efficient coatings can enhance insulation properties, contributing to reduced energy consumption in buildings.
Ultimately, the journey of float glass from production to a cut-to-size masterpiece illustrates the synergy between advanced technology and traditional craftsmanship. The result is a material that not only meets aesthetic and functional requirements but also upholds the highest standards of quality and safety. As float glass continues to evolve, its role in shaping our built environment remains indisputable, solidifying its status as an indispensable component in contemporary design.