Understanding the intricacies of selecting materials for your construction or renovation project is paramount, especially when considering energy efficiency and cost-effectiveness. One of the key components that have gained significant attention is low e glass. Known for its ability to enhance energy efficiency by minimizing heat transfer, low e glass, or low-emissivity glass, is a popular choice among architects and builders. However, understanding the cost per square foot of low e glass is crucial for budget planning and ensuring a high return on investment.
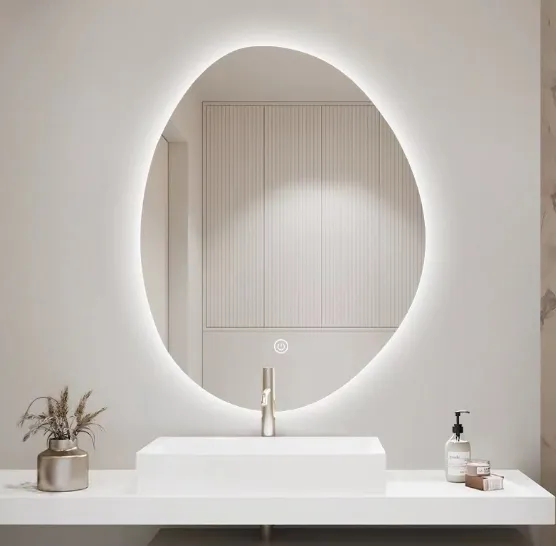
The cost of low e glass per square foot can vary significantly based on several factors, each contributing to its overall value and performance. On average,
prices can range from $10 to $15 per square foot. However, this is a rough estimate, and actual prices may fluctuate based on the type of low e coating, size of the glass, and the geographic location of the project.
One critical determinant of the cost is the type of low e coating applied to the glass. There are two primary types of coatings passive low e coatings and solar control low e coatings. Passive low e coatings are designed to reflect heat back into the room, making them ideal for colder climates. Solar control low e coatings, on the other hand, are optimal for warmer climates as they reflect the sun's heat outward, helping maintain a cooler indoor environment. The choice between these coatings depends heavily on the project's environmental conditions and energy efficiency goals.
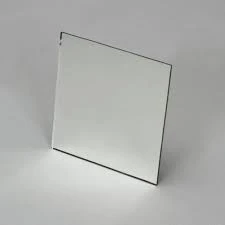
Apart from coatings, the glass size and thickness also impact the cost. Larger or thicker glass panels may cost more due to the increased materials and manufacturing processes involved. Additionally, custom sizes or shapes could further drive up costs due to the need for specialized production techniques.
Geographical factors can also influence the price per square foot of low e glass. In regions where manufacturing facilities are nearby, logistics and transportation costs might be lower, potentially reducing the overall expense. Conversely, remote areas might face higher costs due to shipping and handling complexities.
cost of low e glass per square foot
Moreover, inflation and market conditions at the time of purchase can influence pricing. Economic factors such as the availability of raw materials, demand fluctuations, and technological advancements in glass manufacturing may also impact costs. Staying informed about market trends and price forecasts can help in making more cost-effective purchasing decisions.
It's important to understand that while initial installation costs might seem considerable, low e glass offers substantial long-term savings on energy bills, contributing to a reduced carbon footprint and increased comfort within the building. These energy savings often offset the initial costs, delivering value for money over time.
For those considering the use of low e glass, consulting with industry experts can provide deeper insights into the benefits and potential cost savings. Professionals with experience in energy-efficient building materials will offer valuable advice tailored to specific project needs, highlighting the most suitable products and ensuring regulatory compliance.
Ensuring trustworthiness and authority in selecting low e glass also involves verifying the supplier's credentials and client reviews. Reputable manufacturers and suppliers with a demonstrated commitment to quality and customer satisfaction can offer assurances that the product will perform as expected, maintaining energy efficiency and durability.
Overall, while the cost of low e glass per square foot is an important consideration, it's essential to align the investment with the broader objectives of sustainability and energy efficiency. By choosing products that meet these criteria, builders and architects not only contribute to an environmentally sustainable future but also realize long-term economic benefits for their projects.