The Cost-Effectiveness of Insulated Glass Units
In the world of construction and architecture, insulated glass units (IGUs) have become a pivotal component for their energy efficiency and aesthetic appeal. An IGU consists of two or more layers of glass separated by a sealed airspace, often filled with a noble gas like argon or krypton, which provides enhanced insulation properties. However, when it comes to insulated glass unit price, several factors come into play that determine the cost-effectiveness of these modern marvels.
One of the primary determinants of an IGU's price is the type of glass used. Low-Emissivity (Low-E) coatings, designed to reduce the amount of ultraviolet and infrared light that passes through the glass while allowing visible light to enter, are more expensive than standard glass but contribute significantly to energy savings over time. Furthermore, the number of glass layers and the thickness of each pane also influence the final cost. More layers and increased thickness typically result in higher insulation performance but at a higher price point.
The frame material and design of the IGU also affect its cost. Common frame materials include vinyl, wood, and metal, each with varying degrees of insulative properties and price tags. Vinyl frames tend to be the most affordable option, whereas premium wood or specialized metal frames can drive up the cost substantially. Additionally, the complexity of the frame design, such as intricate patterns or unique shapes, can add to the manufacturing difficulty and thus increase the price.
Another critical factor in determining the price of an IGU is the size of the unit
Another critical factor in determining the price of an IGU is the size of the unit
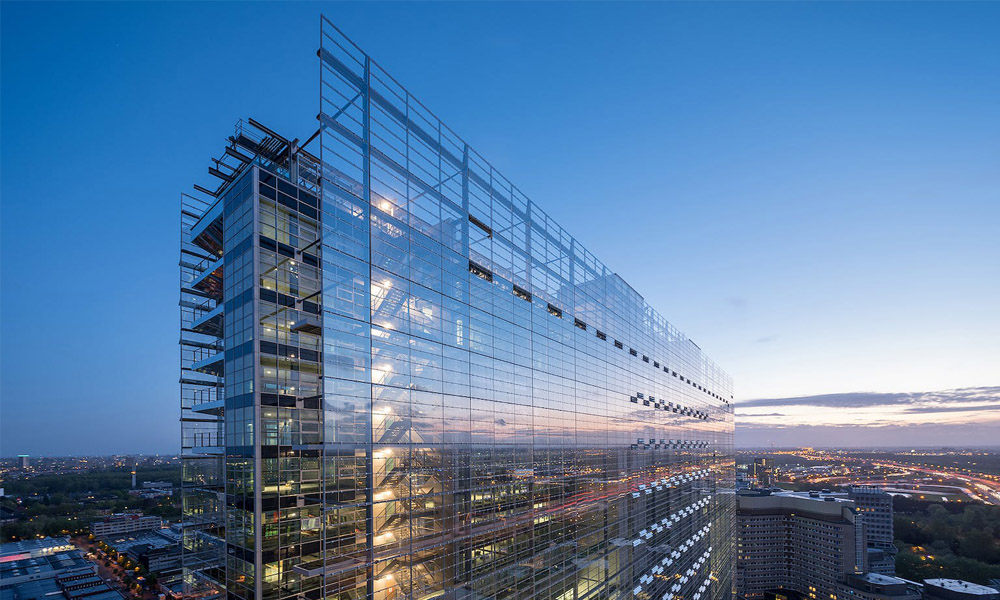
Another critical factor in determining the price of an IGU is the size of the unit
Another critical factor in determining the price of an IGU is the size of the unit
insulated glass unit price. Larger units require more material and may need specialized installation techniques, which can escalate costs. Moreover, custom sizes or shapes often entail additional charges for the bespoke manufacturing process.
Transportation and installation costs must not be overlooked. The distance between the manufacturer and the building site can impact freight expenses, and the complexity of the installation, such as high-rise buildings or difficult-to-reach locations, can increase labor costs.
When considering the insulated glass unit price, it is essential to weigh the initial investment against long-term savings. High-performance IGUs might carry a higher upfront cost but can lead to substantial energy savings throughout their lifespan. This translates into lower heating and cooling bills, increased comfort within the building, and potential tax credits or rebates for energy-efficient upgrades.
In conclusion, the price of insulated glass units reflects a blend of materials, technology, design, and logistics. While the upfront costs may seem daunting, the benefits in terms of energy efficiency, comfort, and potentially increased property value make IGUs a wise investment for both commercial and residential projects. As with any significant purchase, careful consideration of all factors involved is key to ensuring that the insulated glass unit price aligns with both budgetary constraints and long-term objectives.