Tin bath float glass, marking a revolutionary evolution in the glass manufacturing industry, has transformed from a historical curiosity into a contemporary marvel in product applications. Harnessing the precision of modern technology, tin bath float glass is produced by flowing molten glass onto a bed of molten tin, a process that yields perfectly uniform and exceptionally clear glass sheets. This technique, perfected in the mid-20th century, remains unparalleled in its ability to produce high-quality glass for architectural, automotive, and various high-tech uses.

The experience of utilizing tin bath float glass in various sectors has proven time and again its superiority over other glass types. From the perspective of construction and design, architects and builders highly value its flawless finish and structural uniformity. The uniform thickness and immaculate surface provide not only aesthetic appeal but also enhance the structural integrity of buildings. Skyscrapers adorned with expansive surfaces of tin bath float glass benefit from reduced weight variability and increased load-bearing capacity, translating to more stable and durable structures.
In the automotive industry, tin bath float glass has become the cornerstone material for windows and other glass components. Its production technique ensures the minimization of inclusions and distortions, key factors that contribute to improved optical clarity and higher safety standards. This glass type significantly enhances driving comfort and reduces distortion, offering drivers a clear and unobstructed view, which is paramount for safety.
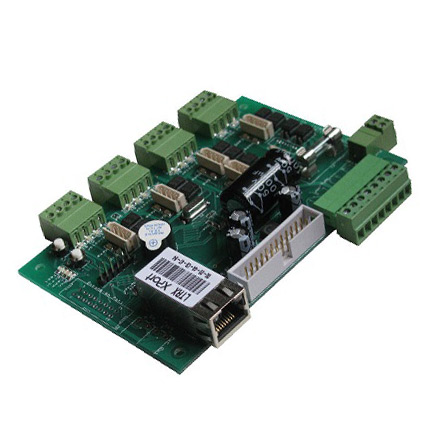
Expertise in the production and application of tin bath float glass is continually advancing, driven by an unwavering commitment to quality and innovation. Manufacturers invest heavily in research and development to push the boundaries of what tin bath float glass can achieve in terms of energy efficiency and environmental friendliness. Innovations such as low-emissivity (Low-E) coatings enhance the thermal performance of glass surfaces, making buildings more energy efficient by reducing heat transmission. This not only contributes to sustainability efforts but also offers economic benefits by lowering heating and cooling costs.
tin bath float glass
Authoritativeness in the realm of tin bath float glass is commanded by industry leaders and organizations that set stringent quality standards. Certification by recognized bodies such as the Insulating Glass Manufacturers Alliance (IGMA) or the Glass and Glazing Federation (GGF) serves as a testament to the enduring quality and reliability of the products. Collaborations between academic institutions and glass manufacturers further bolster authoritative insights, leading to advancements in technology and new application possibilities.
Trustworthiness is foundational in client relationships within the float glass industry. End-users, ranging from individual consumers to large corporations, rely on transparency and integrity from suppliers and manufacturers. Trust is cultivated through extensive testing and stringent quality controls that ensure each glass sheet meets the highest safety and performance standards. Customer feedback and testimonials also play a pivotal role, reflecting the real-world success and satisfaction derived from using tin bath float glass.
In conclusion, the unique properties and benefits of tin bath float glass have made it an indispensable material in modern-day applications. From enhancing the structural stability of high-rise buildings to providing safety and clarity in automobiles, its uses are as diverse as they are essential. As the product continues to evolve, driven by expert innovation and authoritative guidance, tin bath float glass will undoubtedly remain at the forefront of the glass manufacturing industry, renowned for its superior quality and reliability.