The Art and Science of Float Glass Manufacturing
Float glass manufacturing, a technological marvel of the modern era, stands at the intersection of art and science. This process, pioneered by Sir Alastair Pilkington in 1952, has revolutionized the way we produce high-quality, transparent glass used in everything from windows to television screens.
At the heart of float glass production lies the concept of floating molten glass on a bed of molten tin. In this process, raw materials such as silica sand, sodium carbonate, and limestone are first melted at temperatures exceeding 1,500 degrees Celsius. The resulting molten glass is then fed onto a shallow pool of molten tin, where it spreads out evenly due to its own weight and surface tension. As the glass moves along the tin bath, it begins to cool and solidify, forming a continuous ribbon of consistent thickness.
The beauty of float glass manufacturing lies not only in its simplicity but also in the quality of the product. The process naturally produces a smooth surface on both sides of the glass, eliminating the need for grinding and polishing. This makes float glass an exceptionally versatile material with applications ranging from architectural features and automotive windows to photovoltaic panels and sophisticated electronic displays.
However, the science behind float glass is just as compelling as its aesthetic qualities
However, the science behind float glass is just as compelling as its aesthetic qualities
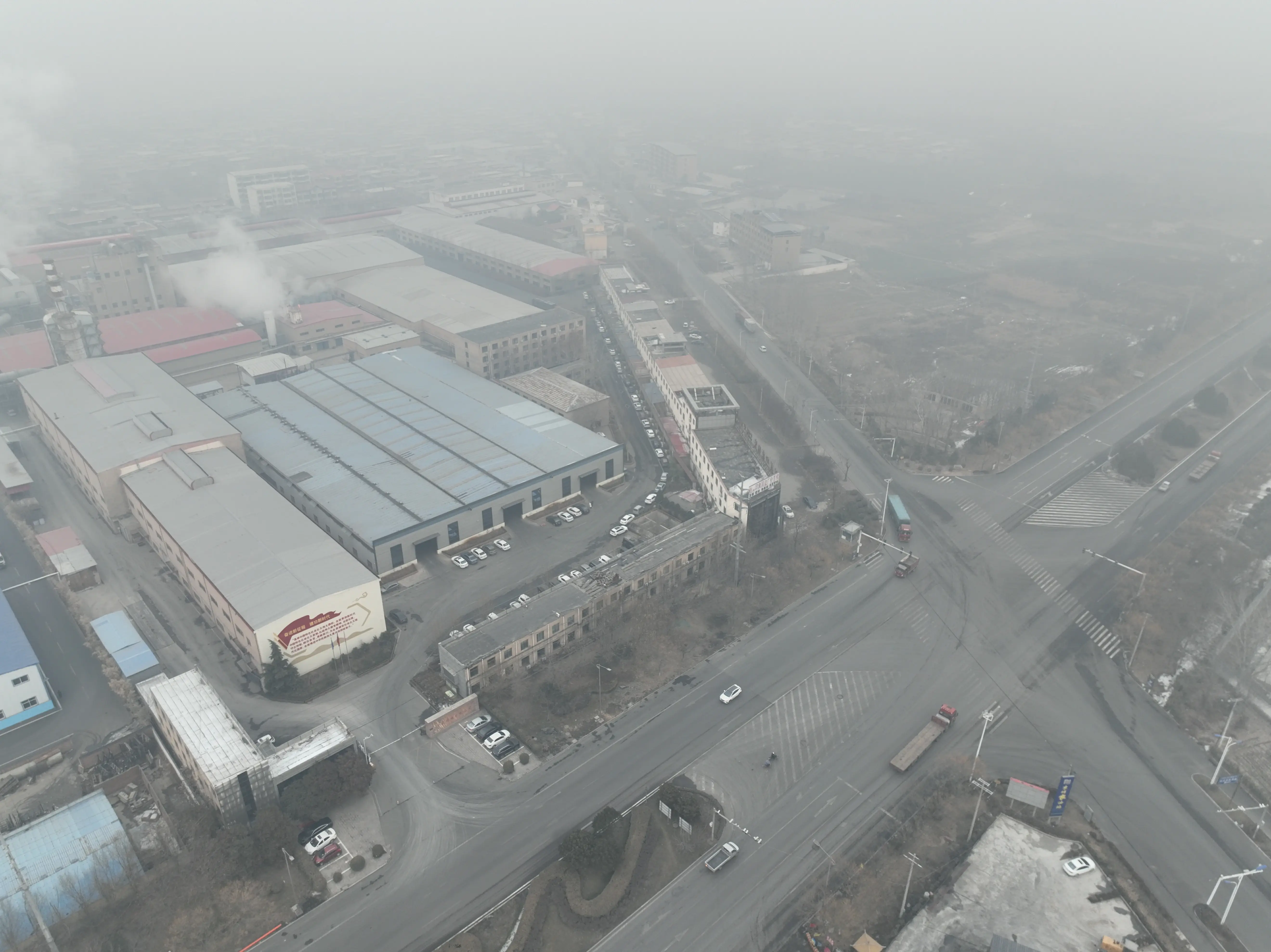
However, the science behind float glass is just as compelling as its aesthetic qualities
However, the science behind float glass is just as compelling as its aesthetic qualities
float glass manufacturers. The interplay between the molten glass and tin requires precise control of temperature, speed, and environment to ensure optimal results. Advanced machinery and rigorous quality checks are integral to maintaining consistency and reducing imperfections.
Moreover, float glass manufacturers continuously strive to improve energy efficiency and reduce environmental impact. Innovations in furnace design, heat recovery systems, and tin recycling have made the float glass process more sustainable over the years.
In conclusion, float glass manufacturing is a testament to human ingenuity and our quest for perfection. It's a delicate dance of physics and chemistry, performed at temperatures that would otherwise be unimaginable. The end result is a product that graces our buildings, protects our vehicles, and enables our technology, all while telling a story of innovation and craftsmanship.