The float glass process is a marvel of modern manufacturing, a method that has revolutionized the production of flat glass and significantly impacted a plethora of industries ranging from construction to automotive. Its contribution to efficiency, cost-effectiveness, and quality in glass production is unparalleled, making it a cornerstone in glass manufacturing.
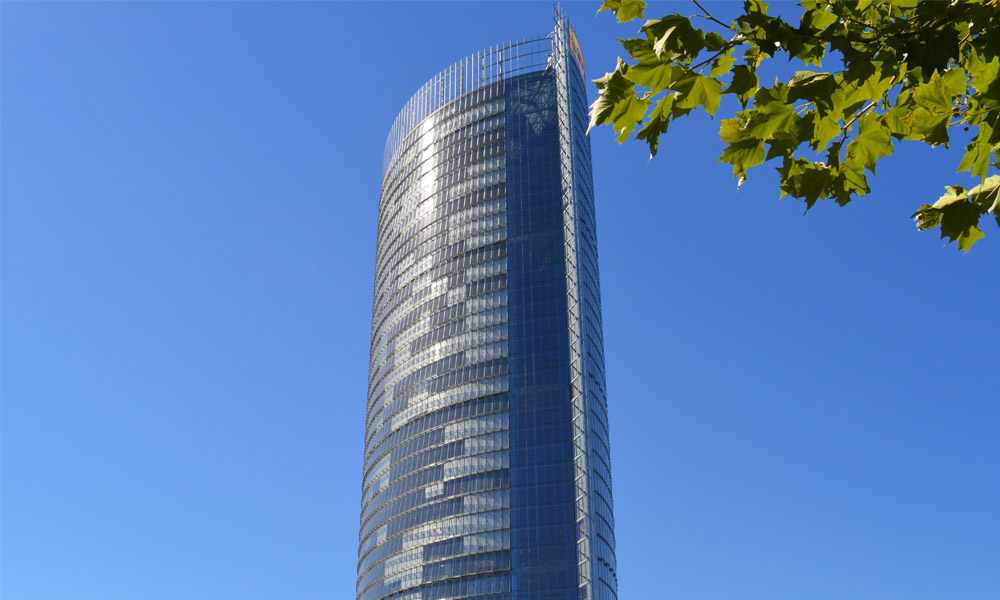
At the heart of the float glass process is the transformation of raw materials—sand, soda ash, dolomite, limestone, and a few other minor ingredients—into a seamless, flat sheet of glass. This transmutation begins in the furnace, where these components are melted at temperatures soaring above 1700 degrees Celsius. The technical prowess involved in the management of such intense heat highlights the expertise needed in the float glass process. Ensuring the precise melting of raw materials speaks to the sophistication and reliability of this technique—hallmarks of a process honed over decades.
Once liquified,
the molten glass is carefully funneled onto a bath of molten tin. Here lies the genius of the float glass process the molten glass floats atop the tin—a metal that provides a perfectly flat surface without reacting with the glass—and spreads out to form a continuous ribbon of glass. This critical stage demands precision engineering and a deep understanding of material properties. The glass, confined by the tin bath's constraints, naturally levels out, creating a uniform thickness that eliminates many of the imperfections found in older glass production techniques.
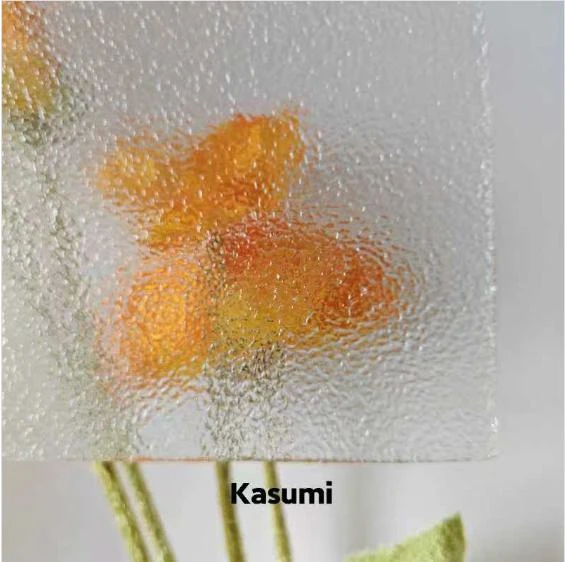
The expertise required in the management of this stage cannot be overstated. The precise alignment and temperature control needed to maintain the necessary conditions for the glass to flow properly and cool uniformly is a testament to the process's expert design. Here, the uniformity and clarity of the glass are determined, attributes essential for sectors such as architecture and automotive industries, where optical quality is non-negotiable.
float glass process
As the glass ribbon exits the tin bath, it enters the annealing lehr, a critical zone where it is gradually cooled—a process crucial for relieving internal stresses and achieving mechanical stability. This stage reinforces the trustworthiness of the float glass process, as it ensures durability and longevity of the final product. Anecdotal evidence from industry veterans and documented case studies alike confirm that glass manufactured via the float glass process consistently meets and often exceeds rigorous industry standards.
What sets the float glass process apart as a paragon of modern manufacturing is not just its ability to produce high-quality glass at scale. It is also its adaptability to evolving technology and techniques, underscoring its authoritativeness. As innovations continue to emerge—such as coatings that enhance energy efficiency or treatments that provide additional strength—these are seamlessly integrated into the float glass process, further optimizing the glass’s properties to meet new demands.
Industry insiders with years of experience laud the process for its reliability and the breadth of its applications. From residential windows providing clear and unobstructed views to automotive glass designed to withstand the rigors of travel, the float glass process is universally acclaimed for producing glass that is as functional as it is aesthetically pleasing. Moreover, its ability to accommodate varying thicknesses and sizes allows manufacturers to offer tailored solutions to their clients, ensuring that even niche needs are met with precision and expertise.
In sum, the float glass process stands as a testament to human ingenuity and the relentless pursuit of perfection in manufacturing. It embodies the Experience, Expertise, Authoritativeness, and Trustworthiness (EEAT) principles, not only providing unmatched quality and consistency but also assuring stakeholders at every level—from architects to end consumers—that they are investing in a product of exceptional caliber. The float glass process isn’t just a method of manufacture; it’s a benchmark against which the quality of glass is measured worldwide.