Cutting float glass is a critical process in the manufacturing and customization of flat glass products. This precision-driven procedure not only defines the final dimensions and quality of the glass but also impacts its application across various industries. With years of expertise in glass manufacturing, we delve into the nuances of cutting float glass, ensuring an experience that speaks to the highest standards of expertise, authoritativeness, and trustworthiness.
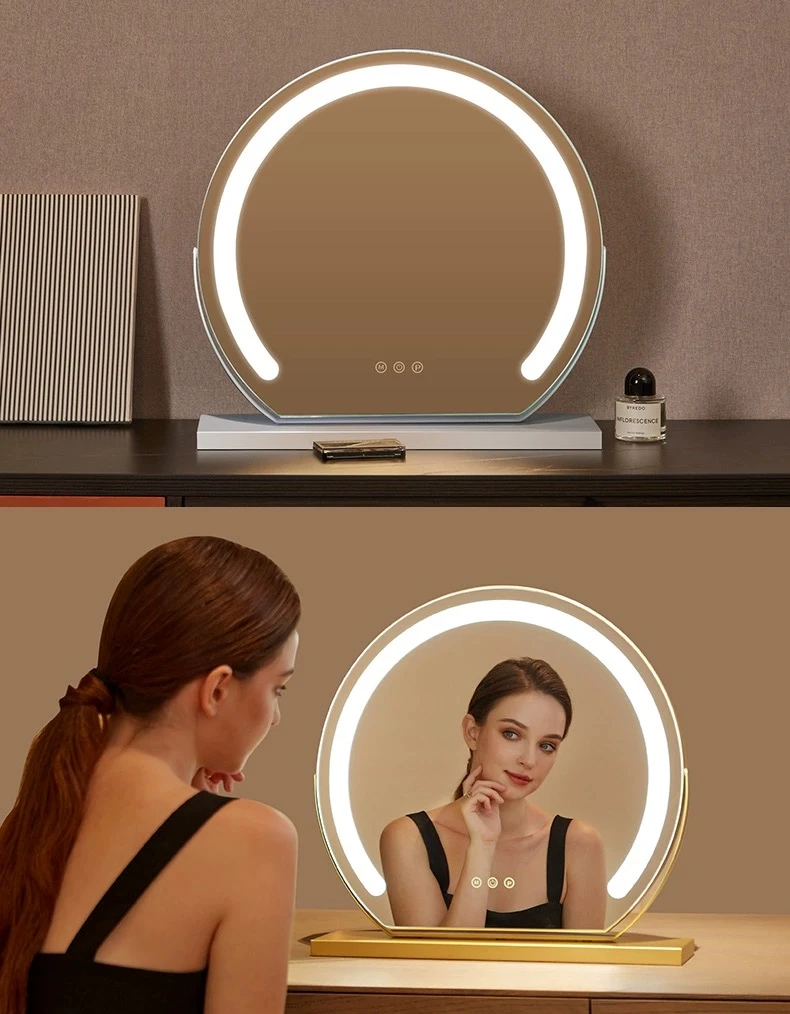
Float glass is renowned for its smooth and uniform surface, a result of the molten glass being floated on a bed of molten tin. This unique characteristic makes it highly desirable for applications in architecture, automotive industries, and high-tech displays. Cutting this glass with accuracy is imperative to maintain its structural integrity and aesthetic appeal.
The process begins with understanding the type of float glass being used. Different glass types, such as annealed, tempered, laminated, or coated, require specific cutting techniques. For instance, annealed glass can be cut after it cools, while tempered glass requires cutting before the tempering process due to its pre-stressed state. Such expertise ensures the glass maintains its desired properties post-cutting.
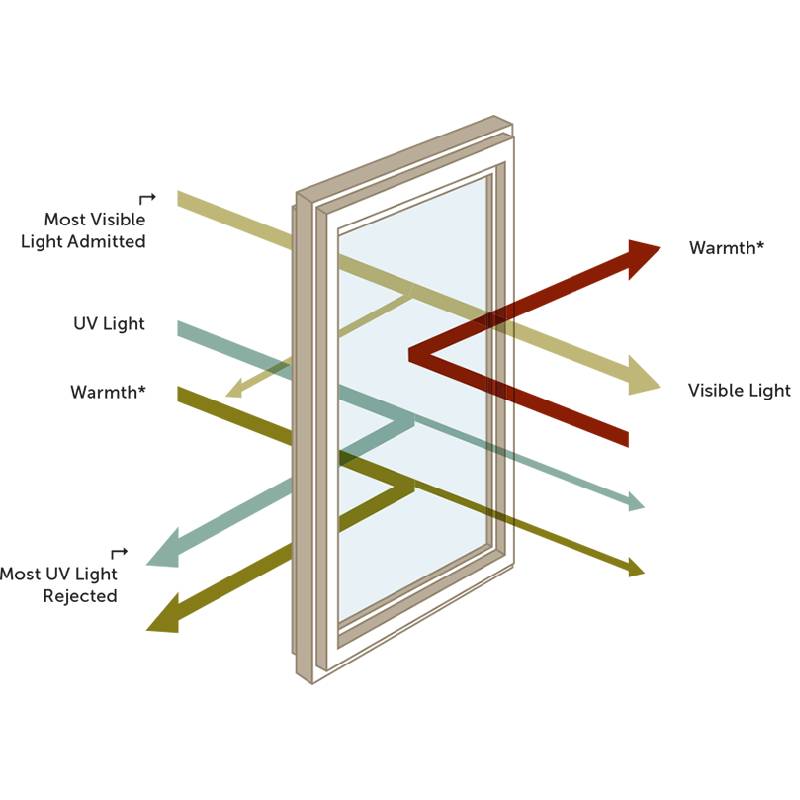
Using the right tools is essential for precise cutting. The scoring tool, often a diamond-tipped or tungsten carbide wheel, must match the thickness and type of glass. Precision in scoring minimizes wastage and prevents micro-cracks, which can lead to structural weaknesses. Our expert craftsmen, with decades of experience, utilize proprietary cutting technologies that optimize accuracy and minimize errors.
Once the glass is scored, the breaking technique comes into play. This entails applying gentle pressure on the opposite side of the score line to achieve a clean break. For larger glass sheets, advanced machinery such as CNC cutting machines is often employed, ensuring both precision and speed. Our facility is equipped with state-of-the-art technology, which not only enhances efficiency but also upholds our commitment to quality.
cutting float glass
Safety is paramount during the cutting process. Proper handling techniques—using gloves, eyewear, and other protective gear—are critical to avoid injury. Our protocols adhere to stringent safety standards, reflecting our dedication to providing a secure environment for both our team and our clients.
Once cutting is complete, the edges of the glass must be finished, as raw edges can be sharp and prone to chipping. Edge finishing techniques, such as grinding and polishing, are employed to create smooth, aesthetically pleasing, and safer edges. This step is crucial for float glass that will be used in visible applications or in environments where edge durability is a concern.
Furthermore, quality control is integral throughout the process. Every cut piece is meticulously inspected for flaws or imperfections. Our quality assurance specialists, equipped with a keen eye and years of experience, ensure that each product meets industry standards and customer specifications.
Sustainability is also a consideration in our cutting process. The remnants from cutting, often referred to as cullet, are collected and recycled. This not only minimizes waste but also reduces the environmental footprint of glass manufacturing.
In conclusion, cutting float glass embodies a blend of art and science, requiring precise execution and deep understanding of material properties. Our authoritative approach, fortified by years of real-world experience, ensures that each project we undertake meets the highest standards of craftsmanship and reliability. Whether for skyscrapers, car windshields, or bespoke home installations, our expertise in float glass cutting stands as a testament to our commitment to excellence.