Float glass has earned a remarkable position in the world of fused glass artistry, whether you're a seasoned professional or just starting in this mesmerizing craft. Its reputation stands on its uniformity and smooth surface, which makes it a preferred choice among creative artisans. For those venturing into the art of glass fusing, understanding the intricacies of float glass can lead to astonishing artistic achievements.
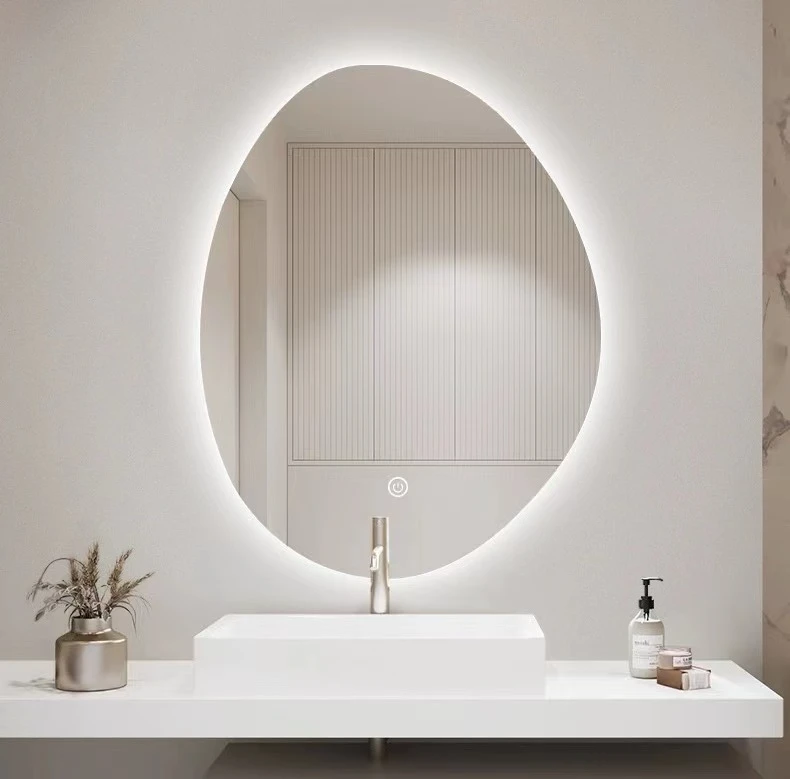
Float glass is typically manufactured by floating molten glass on a bed of molten tin, creating smooth, flat surfaces without the need for polishing. This characteristic differentiates it dramatically from other glass types, making it ideal for various applications in fusing. Artists are drawn to its clarity and ease of use, enabling them to explore a broad spectrum of artistic expressions.
When considering float glass for fusing, it is crucial to acknowledge that its particular composition and thermal properties may vary. These variations can influence the outcome of a fused glass project. One important aspect is the differential in the coefficient of expansion (COE) between float glass and other art glasses, which must be compatible to avoid cracks during the cooling process. Understanding this property is essential for achieving seamless results in fused art pieces.
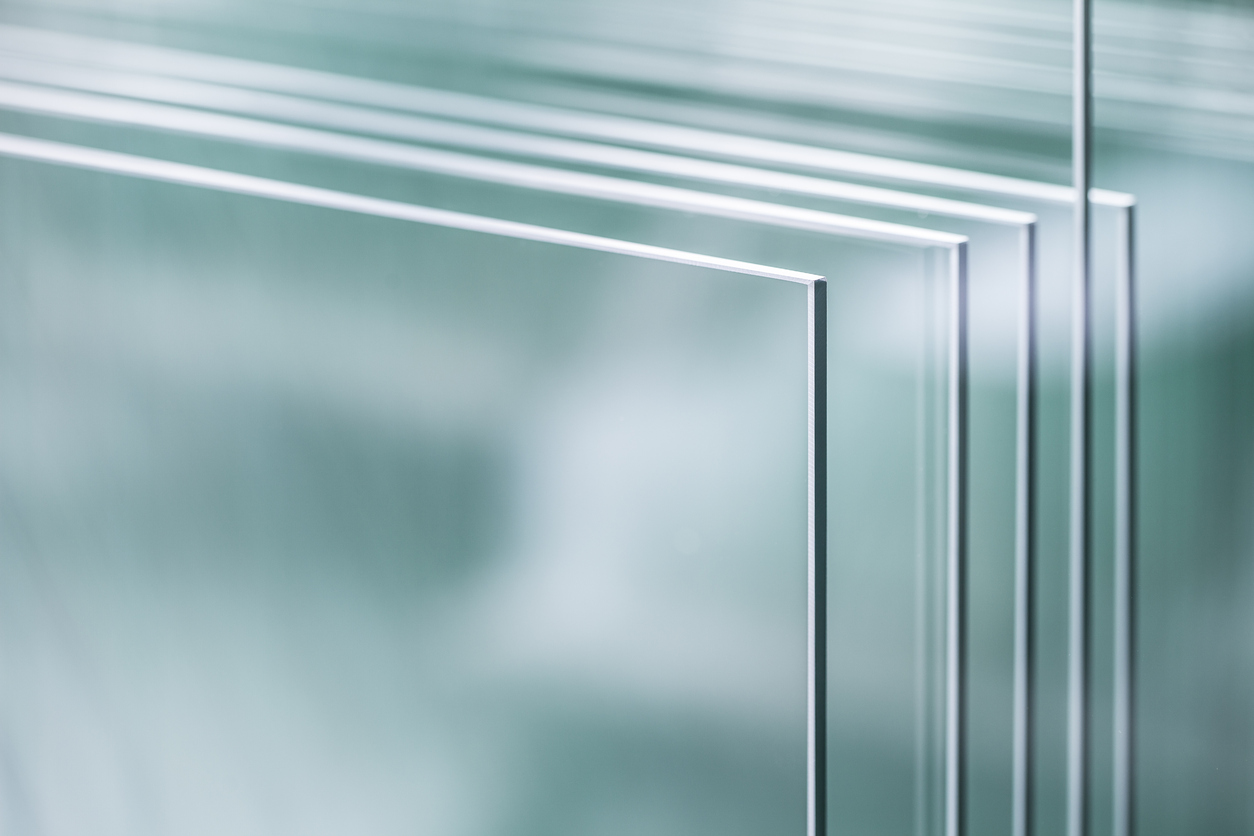
For experienced glass fusers, float glass serves as both a canvas and a versatile medium. It can act as a base layer for intricate designs or serve as the main component in minimalist art, where its delicate appearance adds to the piece's allure. Float glass's versatility is also highlighted in architectural elements, such as windows and doors, where fusing techniques can be applied to create unique design features.
The trustworthiness of float glass lies not only in its consistent performance but also in its widespread application across industries. In-depth knowledge of its qualities can position an artist as an expert in this medium, bringing authority to their work and attracting clients seeking quality and innovation. A familiarity with kiln schedules for float glass is a testament to one's competence, ensuring stress-free heating and annealing processes that prevent breakages and maintain the integrity of their creations.
float glass for fusing
Moreover, the ecological footprint of float glass should not be overlooked. As sustainable practices become increasingly significant in artistic communities, float glass offers an environmentally friendly option. Many manufacturers abide by stringent regulations that reduce emissions and promote recycling, aligning with the values of conscientious artists.
Collaboration with manufacturers and suppliers who provide detailed COE specifications can also enhance the safety and precision of projects. Developing relationships with these companies grants access to advanced insights and the latest innovations in glass technology. For artisans eager to expand their expertise, these alliances can be invaluable, providing stability and assurance in their craft.
Marketing a fused glass product reliant on float glass involves emphasizing these superior characteristics—its strength, beauty, and eco-friendliness—offering a competitive edge in the art and architectural markets. As artisans refine their technical and creative skills in float glass fusing, they transform into authoritative figures, trusted not only for their craftsmanship but also for their profound understanding of the material.
The future of float glass in fusing is bounded only by creative imagination. Its potential extends far beyond traditional applications, encouraging artists to push boundaries and experiment with new techniques. As the demand for unique and durable art pieces grows, so does the significance of float glass, ensuring it remains a cornerstone of both traditional and contemporary fused glass arts.